ROTATIONAL MOLDING
Scribner Plastics uses the rotational molding technique to manufacture all our products. Rotational molding is a plastics processing technique ideally suited to producing relatively large, hollow seamless parts which are partially or totally enclosed. While this process has been in existence since the 1930's, the introduction of micronized polyethylene provided the industry with an ideal material for the rotational molding process.
Relative to their size, rotationally molded parts can have thinner or thicker walls than parts made by other processes. The low processing pressure provided by rotational molding has the added advantage of producing parts which are relatively stress free, as compared to other high pressure processes. This advantage is especially important when considering large, load bearing parts in applications which must provide corrosion or stress resistance.
Additional benefits include the ability to tailor surface finish and color requirements to the product and the ability to use metal inserts or integrally molded threads. Deep cavity parts with closely spaced double walls are common and many parts can be molded with little or no draft angle.
In addition to our complete line of motorsports products and shipping containers for the automotive industry, Scribner Plastics has produced custom items as varied as kayaks, bicycle storage lockers, storage tanks and floats for docks.

SCRIBNER PLASTICS - ROTATIONAL MOLDING MACHINES
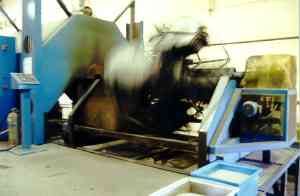
ROTATIONAL MOLDING PROCESS
In rotational molding, a pre-measured amount of plastic material in liquid or powder form is placed in a cavity and the mold is closed. The molding machine then indexes the mold into an oven where the mold and, subsequently the plastic, is brought up to the molding temperature. As the mold is heated, it is rotated continuously about its vertical and horizontal axes, This biaxial rotation brings all the surfaces of the mold into contact with the mass of plastic material. The mold continues to rotate within the oven until all the plastic material has been picked up by the hot inside surfaces of the cavity. The mold continues to rotate until the plastic material densifies into a uniform layer of melt.
While continuing to rotate, the machine moves the mold out of the oven and into a cooling station. Air or a mixture of air and water, cools the mold and the layer of molten plastic material. This cooling process continues until the part has cooled sufficiently to retain its shape. The machine then indexes the mold to the loading and unloading station where the mold is opened and the part removed. A new batch of material is then placed in the cavity, the mold is closed and the process is repeated.